Plastic injection moulding: The problem of black spots
Reiniger SC reduces effort and costs
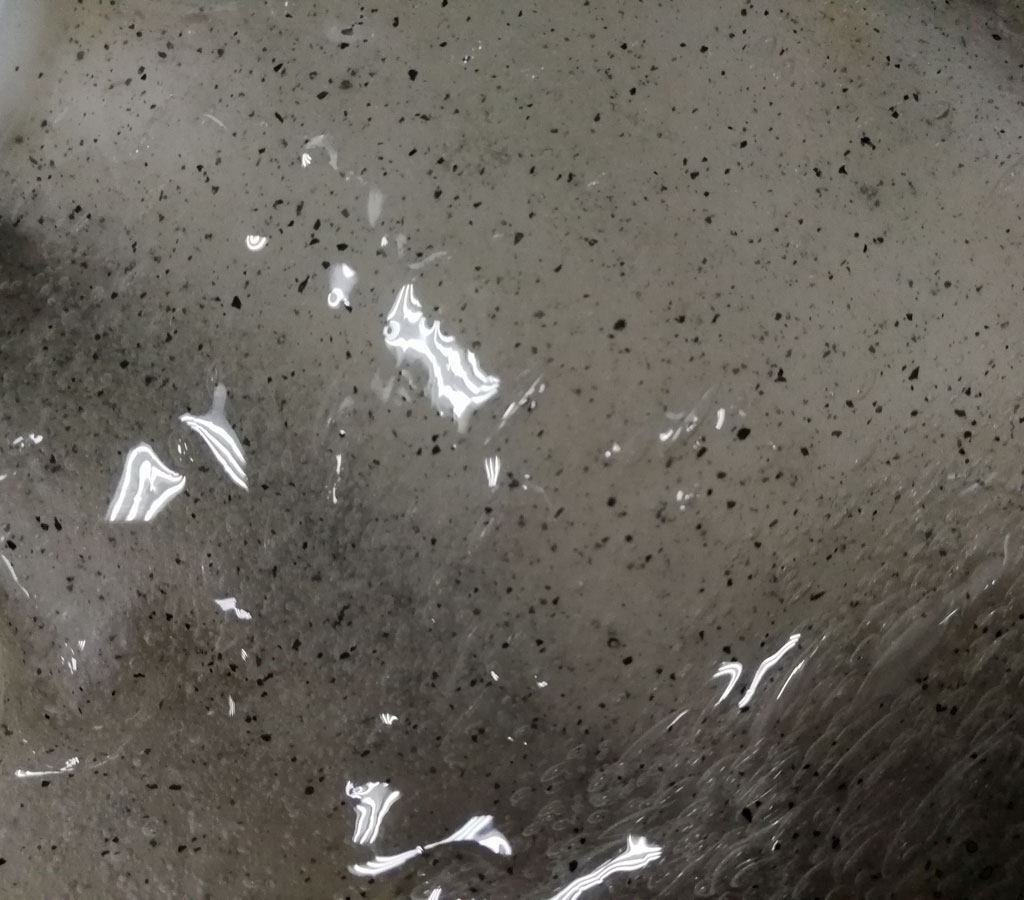
Black spots on or black inclusions in the moulded parts are an annoying, time-consuming and costly problem. The particles are released when starting production and before or during regular cleaning of the screw and cylinder. These particles develop when material carbonises due to overheating, which may occur when the material flow is stopped for a longer time without reducing the temperature in the machine.
During these pauses, the plastic material remains in the plasticising unit and starts to carbonise on the inner wall of the cylinder and on the screw surface. Over time, this layer of carbonised material becomes thicker and thicker until it cracks, and black particles are injected into the mould. When the machine is cleaned, additional pressure is put on this layer due to the volume expansion. The consequence: immediately after cleaning, especially many black spots occur.
This problem can only be solved by removing both screw and nozzle and cleaning them manually. Furthermore, the melt temperature should be reduced during pauses to prevent the material from carbonising on the walls.
Common cleaning procedures support deposits
Cleaning the screw, cylinder and nozzle is a special challenge. Many Asian companies flame the screw and then treat it with a steel brush and sand paper. The cylinder is also cleaned by sanding. The downside: carbonised material can accumulate more easily and faster on the roughened surfaces. Micro-sandblasting and abrasive cleaners destroy the screw’s polished surfaces as well and accelerates the formation of new deposits.
Reiniger SC: gentle, yet highly efficient
From the many customer meetings, we at Buchem know this problem and therefore have developed a simple and gentle solution: firstly, the layer of carbonised material is sprayed with Reiniger SC. Containing highly efficient and concentrated solvents, the cleaner infiltrates the deposits, dissolves the surface and thus reduces the adhesion. Due to the subsequent dry-ice blasting, the material shrinks abruptly and cracks through the high tension. Such a high tension can also be achieved by applying a hot air blower. Buchem’s procedure offers maximum protection when cleaning surfaces. And since the surfaces are not roughened, the formation of new deposits is not accelerated.
Want to know more? We are happy to assist you!